Ingénierie du plus grand aéroport de Chine
Aéroport international de Pékin Daxing

Ce que nous avons livré
-
Intégrer la protection contre l'incendie dans le tissu du bâtiment
-
Élaborer une stratégie de sortie sûre en cas d'incendie
-
Optimisation de la structure du toit de l'aéroport de Daxing pour réduire le poids et les émissions de carbone
Contactez notre équipe
L'aéroport international Daxing de Pékin, en forme de phénix, est devenu un bâtiment emblématique de la capitale chinoise.
Conçu par Zaha Hadid Architects, ADP Ingénierie et l'Institut de conception architecturale de Pékin (BIAD), le terminal a une surface brute de plancher totale de plus de 700 000 m² et peut accueillir 100 millions de passagers par an, soulageant ainsi la pression sur l'aéroport international de Pékin.
Daxing est conçu pour être un super centre de transport pour Pékin. Trois gares ferroviaires souterraines d'une superficie totale de 200 000 m² sont situées sous l'aérogare, et cinq lignes de chemin de fer permettent aux passagers de poursuivre leur voyage.
BIAD nous a désignés comme consultants en ingénierie incendie pour l'ensemble de l'aéroport, et nous a ensuite demandé de procéder à un examen par les pairs et à une analyse de la valeur de la structure du toit en acier pour le siège de la construction du nouvel aéroport de Pékin.
La forme fluide et interconnectée du terminal est une pièce d'architecture étonnante, mais elle pose d'énormes défis en termes de sécurité incendie. Cette situation est compliquée par la plate-forme de transport située en dessous et les espaces interconnectés, qui ont dû être traités comme un seul compartiment coupe-feu massif.
Nos ingénieurs incendie ont adopté une approche basée sur la performance pour concevoir les zones de contrôle incendie de l'aéroport. Nous avons intégré une série de stratégies de protection contre l'incendie, notamment des rideaux de fumée, des volets coupe-feu et des bandes de séparation coupe-feu pour empêcher la propagation du feu et de la fumée d'une zone à l'autre, remplaçant ainsi les murs pleins traditionnels qui affectent la circulation des passagers.
Les zones à haut risque sont entièrement confinées grâce à une construction résistante au feu, et nous avons utilisé le grand atrium central pour contrôler la fumée en utilisant la flottabilité et la dilution.


Une stratégie de sortie intelligente
Les sorties de secours ont représenté un défi majeur en termes de conception. En raison de la taille et du nombre d'occupants, la distance d'évacuation vers l'extérieur est supérieure à 200 m dans la majeure partie de la zone centrale, alors qu'elle devrait être inférieure à 75 m dans un bâtiment standard. Pour atténuer ce problème, nous avons aménagé 29 escaliers de sortie dans la zone centrale, ce qui a permis de réduire la distance de déplacement entre les différents étages et de détourner le flux de piétons pour éviter les goulets d'étranglement.
Les zones de manutention des bagages dans les arrivées présentaient également des risques pour une évacuation rapide. Nous avons donc conçu une stratégie de sortie intelligente pour les zones publiques, en utilisant différents itinéraires d'évacuation en fonction de la localisation d'un éventuel incendie.

Optimisation de la structure du toit
Le toit de l'aérogare est une structure métallique hyperboloïde complexe de grande portée qui couvre plus de 350 000 m². Contenant plus de 170 000 éléments en acier, elle est soutenue par des colonnes géantes en forme de C qui se raccordent parfaitement à la toiture.
Nos ingénieurs, à l'aide d'un logiciel développé en interne, ont étudié la configuration, la charge, les réactions du système de support vertical ainsi que la déflexion et le déplacement de la structure à travers le toit. 420 combinaisons de charges ont été prises en compte et 38 tailles de sections différentes ont été utilisées dans la superstructure, notre analyse montrant des possibilités d'optimisation significatives.
Forts d'une grande expérience dans le domaine des structures métalliques à longue portée et de la conception structurelle, nos ingénieurs ont proposé des stratégies pour les différentes zones du terminal, en améliorant les schémas de fermes de toit et en réduisant les profondeurs structurelles inutiles et le dimensionnement des éléments.
L'efficacité est la clé
Bien que la conception du toit en acier ait déjà été examinée par plusieurs instituts de conception locaux avant notre examen, les stratégies d'optimisation complètes d'Arup ont aidé le projet à réduire davantage le tonnage d'acier, ce qui a permis de réaliser d'importantes économies et de réduire les émissions de carbone.
En intégrant le centre de transport et le terminal au lieu de les placer sur des sites distincts, notre solution permettra d'économiser plus de 1,6 million d'heures de travail pour près de 30 millions de passagers chaque année.

Le saviez-vous ?
m2
GFA
m
nombre annuel de passagers à la capacité maximale
les membrures en acier pour le toit emblématique
ADP Ingeniérie / Zaha Hadid Architects / BIAD / China Airport Construction Co Ltd
Projets
Découvrez d'autres projets dans le domaine de l'aviation :
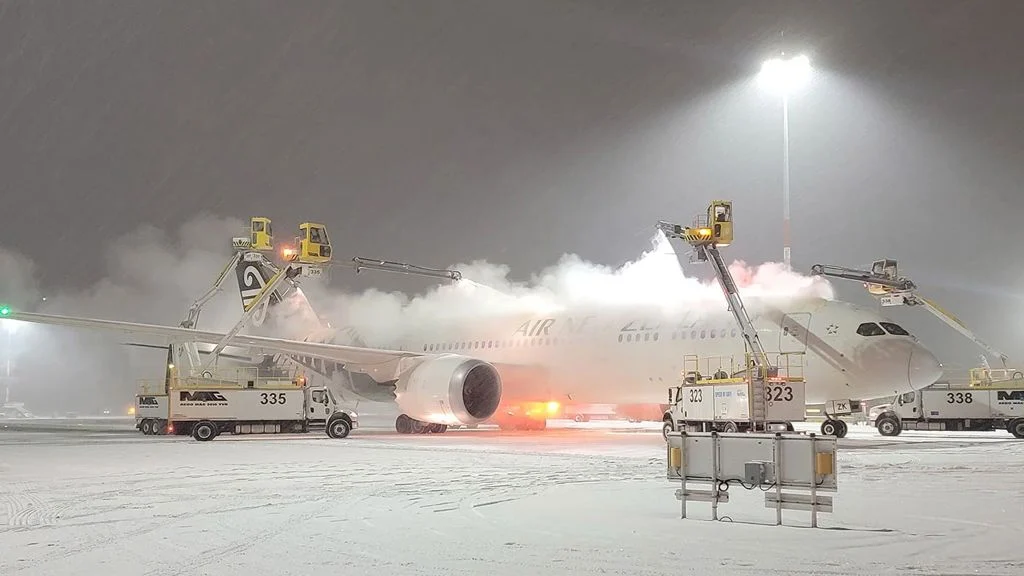
Aider l'aéroport international de Vancouver à se préparer à des conditions météorologiques inattendues
Bilan après action de l'aéroport international de Vancouver, Canada
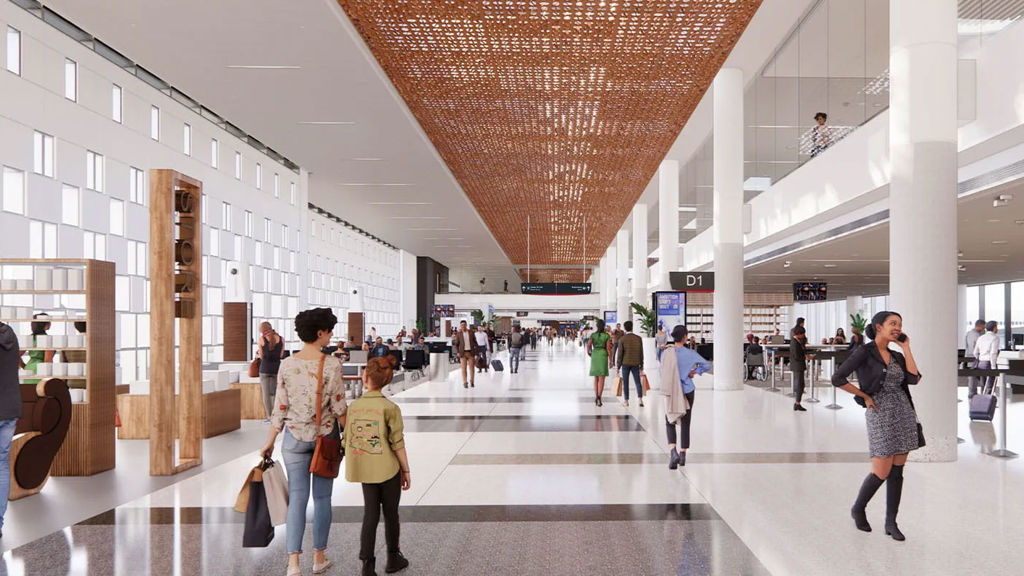
Réaménagement et rénovation sans faille de l'aéroport intercontinental George Bush
Programme de réaménagement du terminal IAH, États-Unis d'Amérique
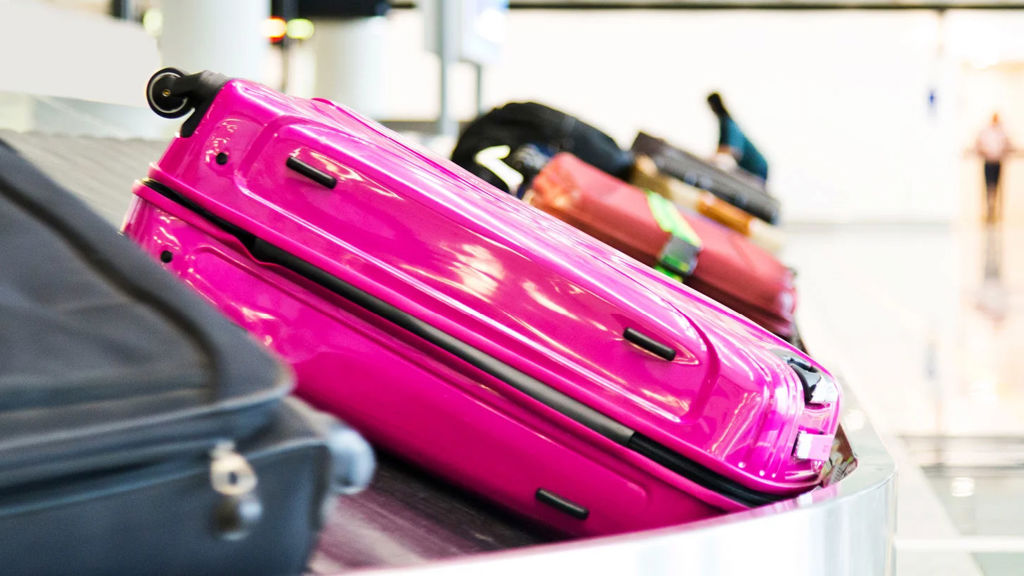
Conception du modèle de préparation opérationnelle de l'aéroport agrandi de Gold Coast
Aéroport de Gold Coast ORAT, Australie
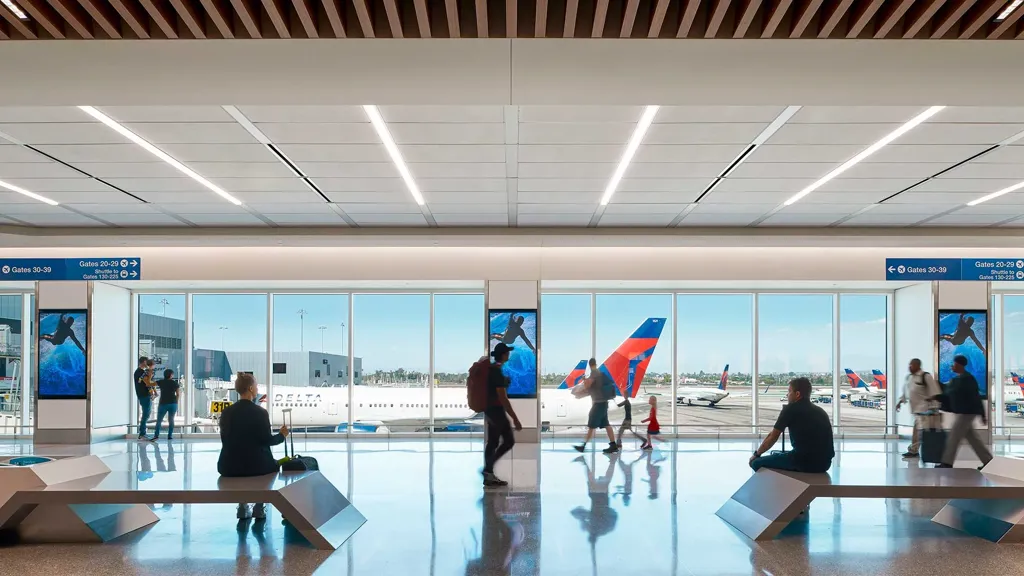
Accélération du projet Delta Sky Way de l'aéroport de Los Angeles avec une équipe pluridisciplinaire de grande envergure
Delta Sky Way à LAX, États-Unis d'Amérique
Prenez contact avec nous
Si vous souhaitez vous entretenir avec l'un de nos experts en aviation sur l'une des questions soulevées sur cette page ou sur une collaboration potentielle, veuillez remplir le formulaire.
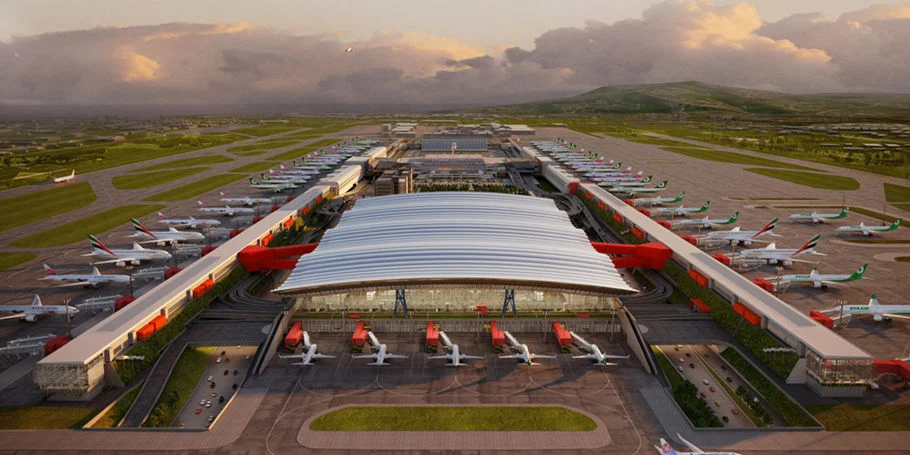