What we delivered
-
Multidisciplinary services for the EPC A-rated building, which has become the tallest commercial building in the country to achieve BREEAM Outstanding.
-
Advanced analytic modelling to design every load-bearing structural element, reducing required steel weight by 25% and saving 5,000 tonnes of CO².
Get in touch with our team
On the corner of two of London’s most prominent streets, 8 Bishopsgate offers 52,900m² of offices, with elevated outdoor terraces, a 200-person auditorium and public viewing gallery at the top of the 50-storey building.
Arup provided multidisciplinary services for the EPC A-rated building, which has become the tallest commercial building in the country to achieve BREEAM Outstanding.
Conceptual alignment between teams
Developed for Mitsubishi Estate London by Stanhope, and designed by Arup and Wilkinson Eyre, 8 Bishopsgate is formed as a series of stacked blocks. This maximises the lettable floor area while protecting views of St Paul’s. Arup provided a range of services based on our international experience designing tall buildings, local knowledge and sustainability capabilities, helping the client and architect achieve their ambitious goals.
At the project’s earliest stage, a collaborative approach between architect and engineer allowed the team to maximise the constrained site’s development area and arrange the massing around the lean component building blocks. In essence, the form was developed to be conceptually efficient from day one.
Optimising operational efficiency
The positioning of building systems can affect how efficiently they function. Arup completed a tipping point service analysis to finetune locations of equipment, considering floor demands and distances. With the reduced size of plant and risers needed, in addition to energy saving benefits, we managed to achieve a slimmer core which increased net lettable area and lower embodied carbon.
Introducing floor-by-floor handling plant rather than a centralised ventilation system will enhance energy efficiency and give greater flexibility to occupiers. Working closely with the client and architect, we located plant areas with a less desirable outlook, balancing the need for access to external air with our objective of delivering a high-quality office space. CO² sensors allow air flow to be adjusted according to demand, rather than a static amount per m². This gives flexibility for multiple occupancy scenarios and empowers the building team to manage fresh air for efficiency and wellbeing.
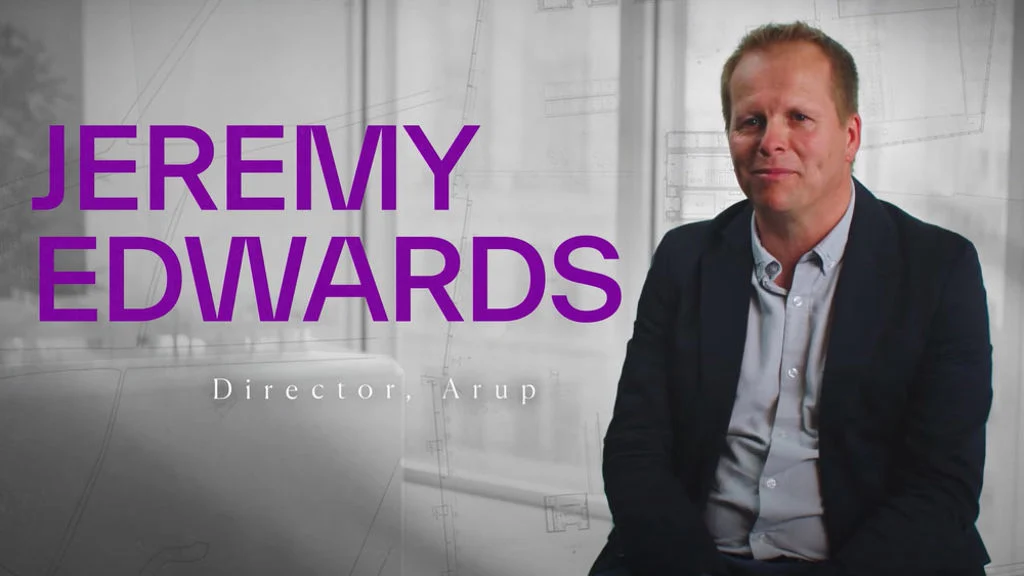
Unlocking opportunities through innovation
In 2018, we validated the feasibility of adding 13 extra storeys to the building, following the changes to planning context with neighbouring schemes. This opportunity led to a re-evaluation of the structural scheme, culminating in a perimeter steelwork bracing solution in the building’s mid-rise section, called the braced box. Rigidly linking the two cores, the braced box allowed them to become slender on the mid-rise and high-rise levels, delivering significant additional net lettable area.
Arup proposed that the braced box would also support a cantilever on the west face, over Bishopsgate. With the architect, we progressed the cantilever to 9m on the south and 5m on the north, whilst extending up. The cantilever accounts for 15% of net internal floor area, key to commercial viability and accentuates the iconic stacked block design.
The level 6 Cantilever represented a particular challenge during construction. In the completed building, the braced box supports this cantilever, yet during the construction the braced box is built after the cantilever. Working with Lendlease and steelwork contractor William Hare to develop temporary works that support this load and ensure that the cantilever’s tip remained within 10mm of its permanent position. We developed a procedure that used five hydraulic jacks to support 700 tonnes of building load, before transferring this load to the permanent structure. During this suspenseful load transfer, the movements stayed within 4mm of modelled predictions, a notable achievement given the scale.
As the project was on site when COVID hit, we swiftly identified opportunities to futureproof the building for future pandemics. This included touch-free lifts and fully ventilated WCs with direct fresh air, rather than recycled air typically found in office buildings. Out flexible initial design made these relatively easy to action.
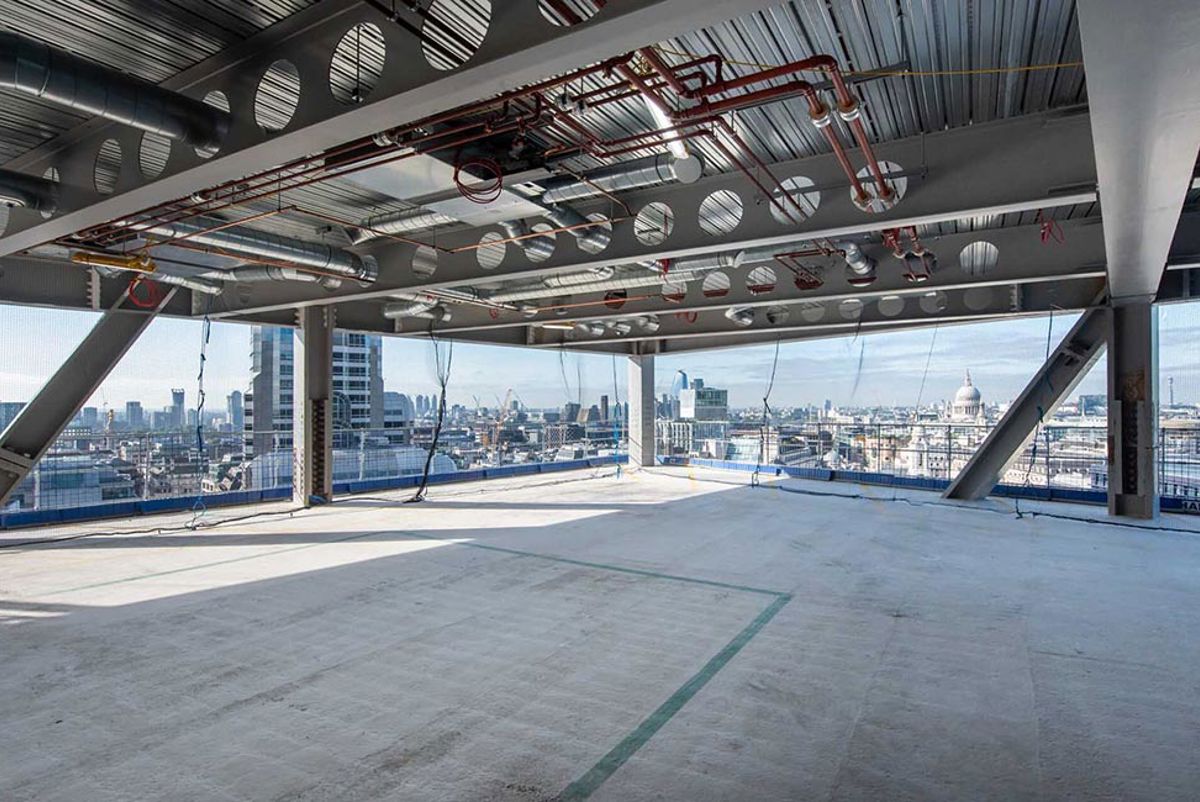
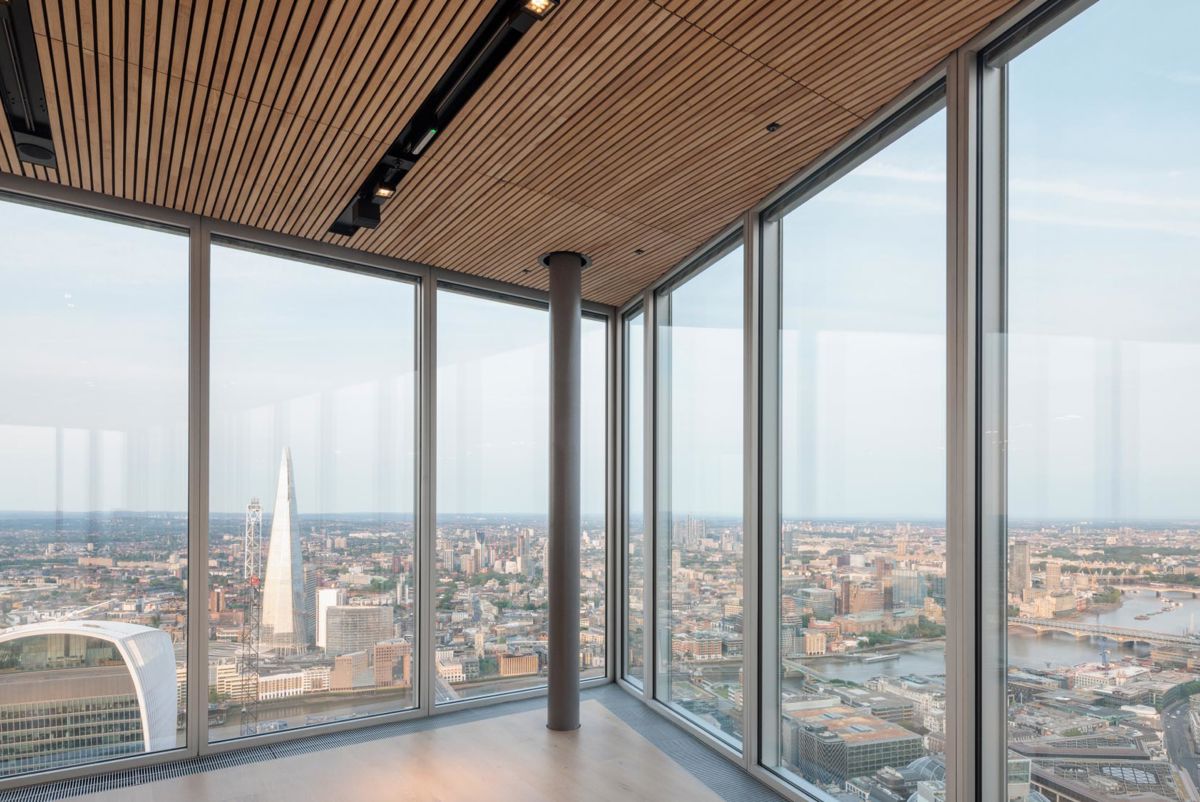

Decarbonisation through detailed design
Using advanced analytic modelling, we designed every structural element for the individual load it would bear across its design life, reducing the required steel weight by 25% and saving 5,000 tonnes of CO2. This approach is more granular than usual for tall buildings, where elements tend to be grouped and designed for the combined load. We saved a further 140 tonnes of CO2 by optimising the beam spacing for the higher levels. This brought cost and programme benefits, with fewer beams to manufacture, unload and lift into place.
Tall towers typically use piled foundations to transfer large vertical loads into the ground. We developed a better way to do this, adopting a pile assisted raft that reduced pile numbers from 89 to 28, saving two months on the construction programme and requiring 3,000 cubic metres less concrete. This was delivered by our integrated team of geotechnical and structural experts who challenged themselves to go beyond the usual.
Façade engineering for comfort and efficiency
To reduce solar gains and glare, we engineered a closed cavity façade system with automated blinds, controlled via a rooftop sensor that tracks the sun’s brightness and positioning. Using an automated system instead of relying on occupiers to use manual blinds reduced the building’s cooling load by half a megawatt, yielding not only operational energy benefits but reducing the embodies carbon and cost of the air conditioning plant.
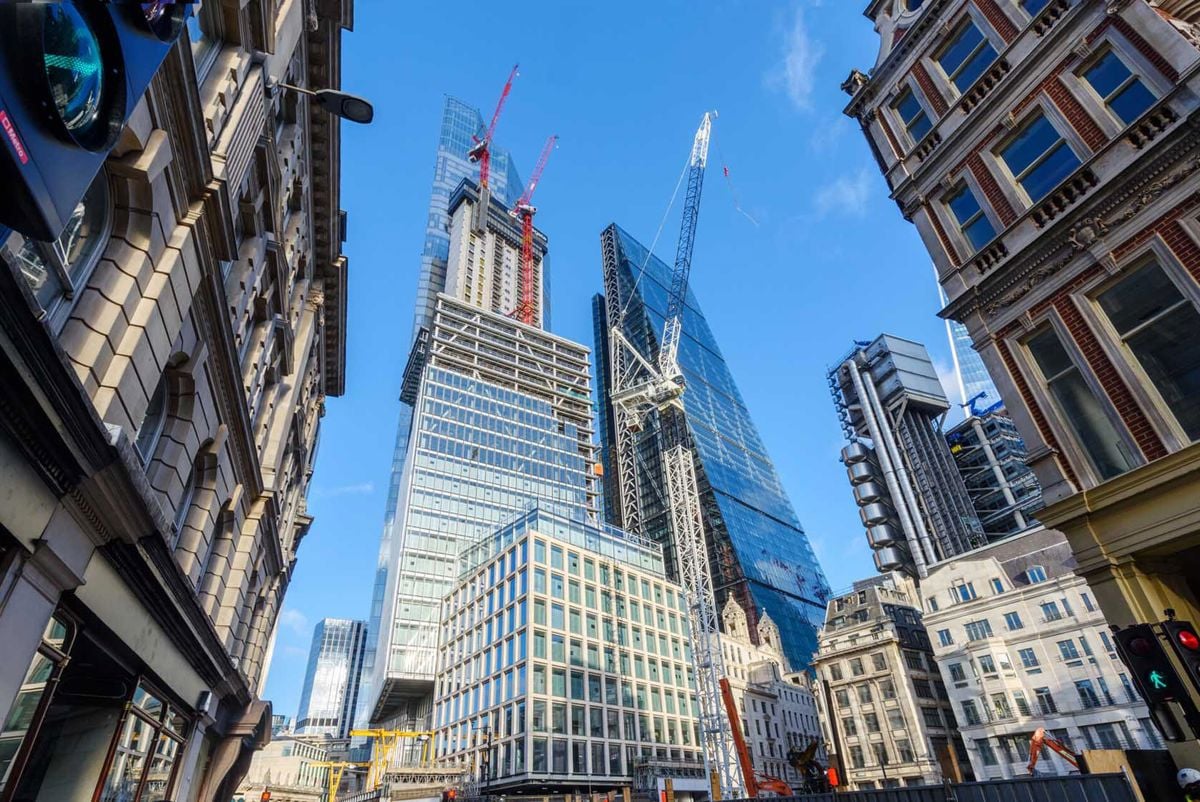
Architect: WilkinsonEyre / Lendlease / Alinea
Projects
Explore more commercial property projects
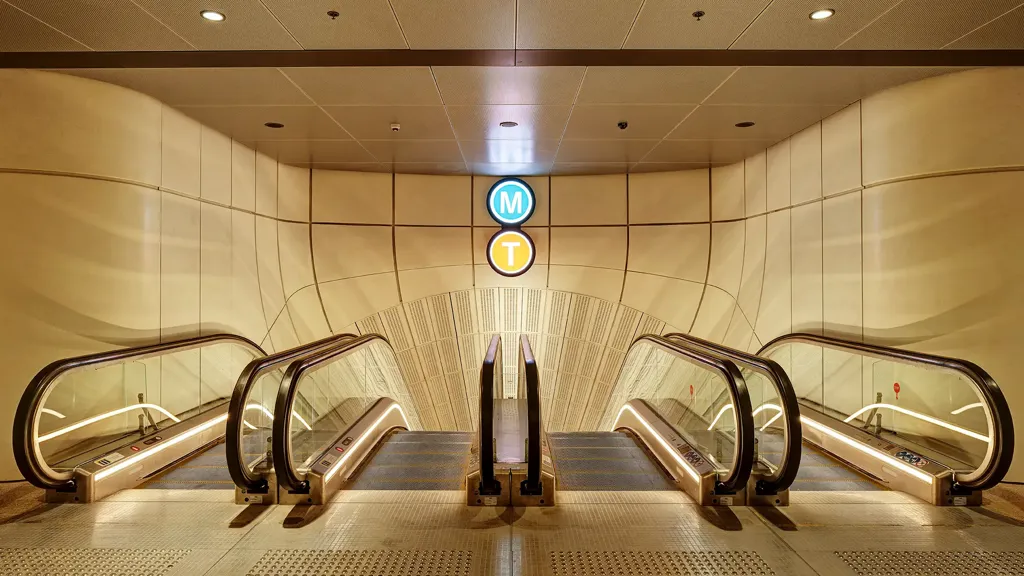
Designing Sydney’s first integrated station development
Sydney Metro Martin Place integrated station development, Australia
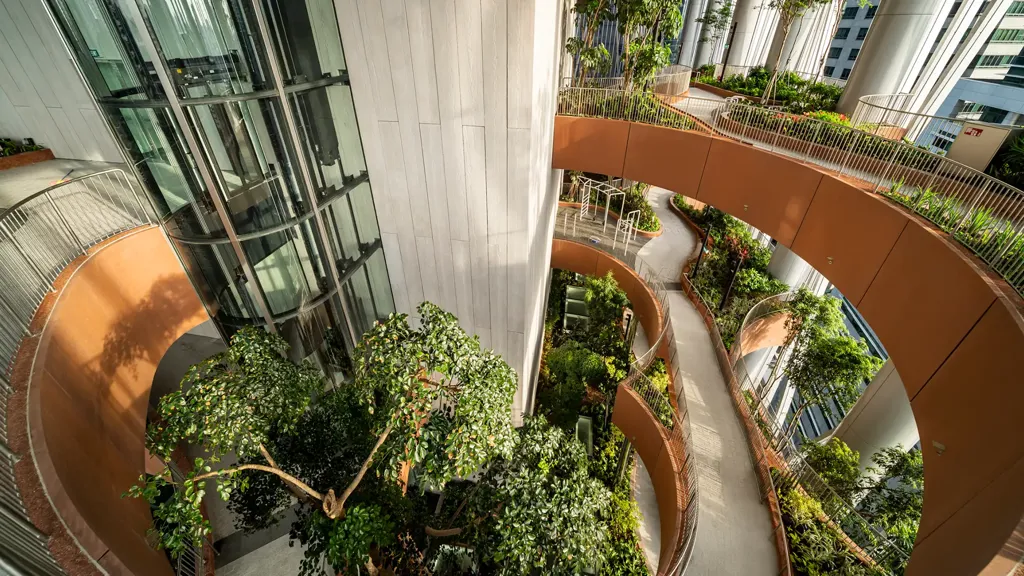
CapitaSpring uses biophilic design to keep people cool and healthy
CapitaSpring, Singapore

Challenging convention to create the next generation of tall buildings
50 Fenchurch Street, United Kingdom
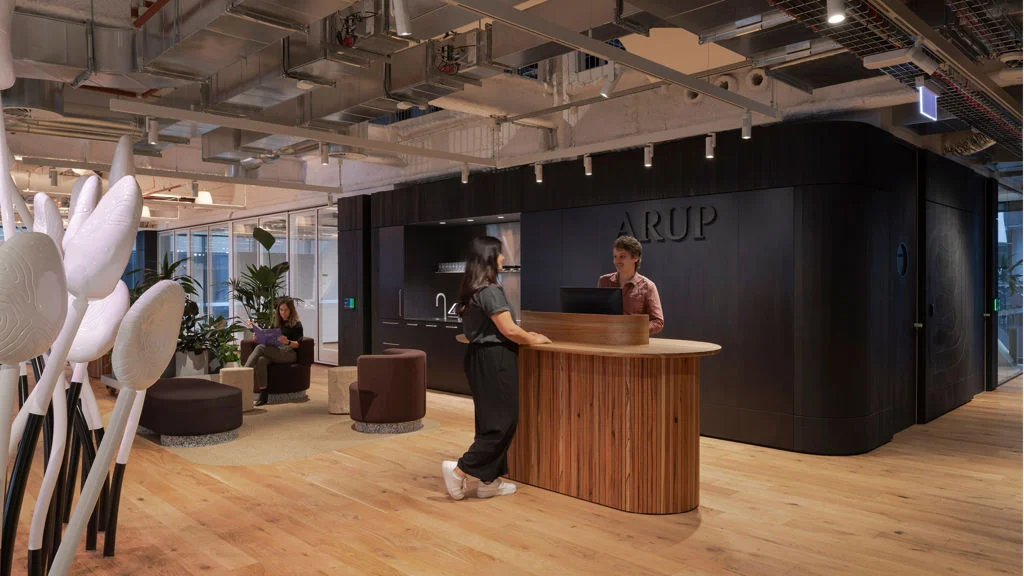
Connecting work, nature and Country
Arup Workplace, WS2, Australia
Get in touch with us
If you'd like to speak to one of our property experts about any of the issues raised on this page or a potential collaboration then please get in touch by completing the form.
