Creating London’s largest all-electric building, designed for hybrid working
80 Charlotte Street

What we delivered
-
An all-electric building with 34% better operational efficiency than Building Regulations and 38% lower embodied carbon than the benchmark for an office building.
-
Engineered one of the leanest floor sandwiches in the world – 600mm slimmer than typical commercial buildings – in partnership with Make.
Get in touch with our team
80 Charlotte Street offers around 40,000m2 of office, retail and residential space, including affordable housing, along with a new public pocket park. Developed by Derwent London and designed by Make architects, it is our first large-scale all-electric building in London and the first major hybrid workplace post-pandemic.
Arup provided multidisciplinary services for the operationally zero carbon building and we are also one of its main occupiers. This supports our sustainability goals and commitment to cities.
Optimising energy performance
The decision to make 80 Charlotte Street all-electric was taken way ahead of its time in 2009. The building uses air source pumps for heating and cooling, avoiding fossil fuels and advancing progress to net zero. It has one of the largest heat pumps in central London, recovering and reusing waste heat via polyvalent units. Electricity on both landlord and tenant sides will be purchased from ringfenced renewable sources and 80m2 of solar thermal panels will pre-heat domestic water.
Our future thinking in 2009 also highlighted how growth in electric vehicle use would lead to cleaner air and quieter roads around the island site. We introduced openable windows at the perimeter and designed systems to operate in mixed mode, reducing energy demand and giving people greater control over their environment. Air conditioning in perimeter areas automatically switches off when windows are open. The reception and atria are naturally ventilated, pulling in outside air, and a highly integrated fresh air strategy uses the atrium to distribute fresh air to floors.
Additional features to enhance operational efficiency include ‘glass in the right place’ façades that allow more natural daylight to flow indoors while minimising solar gain. High air tightness levels of 3m3/h.m2 at 50Pa will also improve energy performance and smart-enabled analytics will give deep insights into building performance.

Reducing embodied emissions
Arup carried out an embodied carbon study early on to identify opportunities to cut emissions. Working closely with Derwent London and Make, we engineered 80 Charlotte Street for lean materials use and flexibility, reducing lifecycle emissions.
Part of the existing fabric from the 1960s building was retained and combined with new-build elements. The façade blends old and new, including original brick façades retained along Whitfield Street. New materials were sustainably sourced, including high recycled content and regional procurement, along with waste minimisation and recycling. This all contributed to the building’s BREEAM Excellent rating.
Designing for new ways of working
80 Charlotte Street is designed to enhance wellbeing and support hybrid working. Base build equipment is smart enabled, so occupiers can not only optimise their systems for efficiency and wellbeing, but also connect people digitally with their workplace.
Three atria at the corners distribute light and air for wellbeing. The publicly accessible pocket park opens new opportunities for people to enjoy nature as part of their daily lives, while a communal roof terrace offers views across north London and the City. Active design features include visible stairs in the reception and spaces for over 300 bicycles. The reception features a café open to the public and space for occupiers to host events and social activities.

We worked in partnership with Make to engineer one of the leanest floor sandwiches in the world – 600mm slimmer than typical commercial buildings. We achieved this by hyper-integrating the structure and services, which enabled the addition of another floor, increasing space by 40,000 sq ft, maximising the potential of the massing and densification that allows an additional 400 people to occupy the site. The structure and services are deliberately visible, celebrating the engineering story.
As the COVID-19 lockdown impacted construction, we collaborated with the site team to witness commissioning and carry out observations remotely. The building was almost entirely prefabricated off site, with kits of parts brought to site and connected together – from precast concrete façades to structural elements such as pipework risers and soffits. This upheld quality, while dramatically reducing on site labour, saving construction time and contributing to the project’s industry-leading safety rate.



As a trusted advisor, Arup collaborated with Gensler and MSMR Architects at DL/78, Derwent London’s new hybrid amenity space on Charlotte Street, providing drop-in working space, meeting rooms, conference facilities, a wellness room and café.
With sustainability and flexibility key, we introduced a wireless Bluetooth lighting system, saving hundreds of metres of cables and allowing lights to be relocated or added without the need to reroute or install extra cables. We also helped implement the first commercial emergency testing and control system via Bluetooth, further reducing embodied carbon by eliminating the need for a large central battery, control modules, cables and lead acid batteries.
Our specialists reduced lighting from a traditional 500lux rule of thumb for illuminance to around 200lux, providing a comfortable working environment for people on devices, and dramatically saving energy. We introduced a variable volume ventilation system that provides fresh air on-demand. This adjusts air flow as spaces become quieter or busier, enhancing both efficiency and wellbeing.
Architect: Make
Projects
Explore more commercial property projects
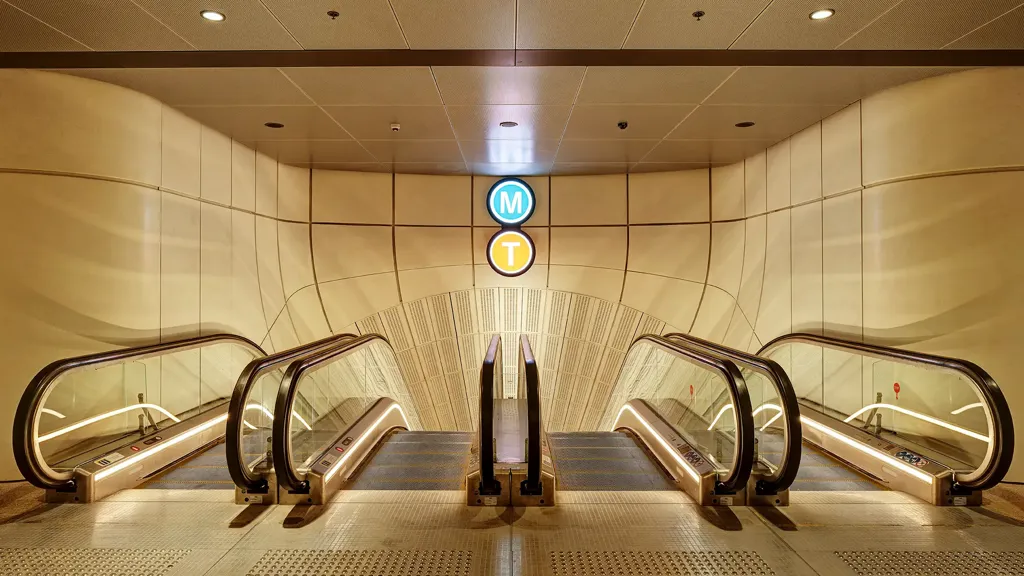
Designing Sydney’s first integrated station development
Sydney Metro Martin Place integrated station development, Australia
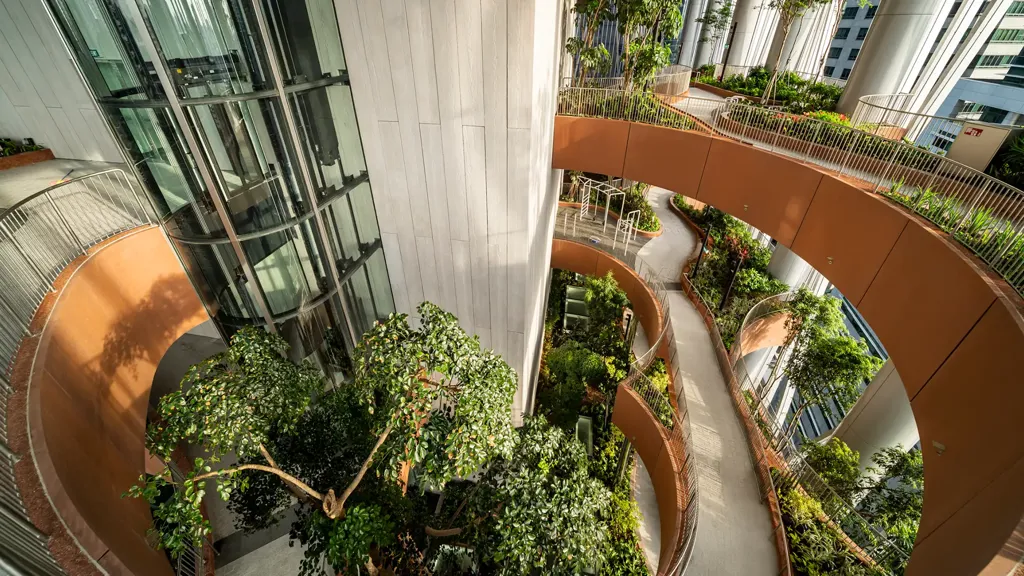
CapitaSpring uses biophilic design to keep people cool and healthy
CapitaSpring, Singapore

Challenging convention to create the next generation of tall buildings
50 Fenchurch Street, United Kingdom
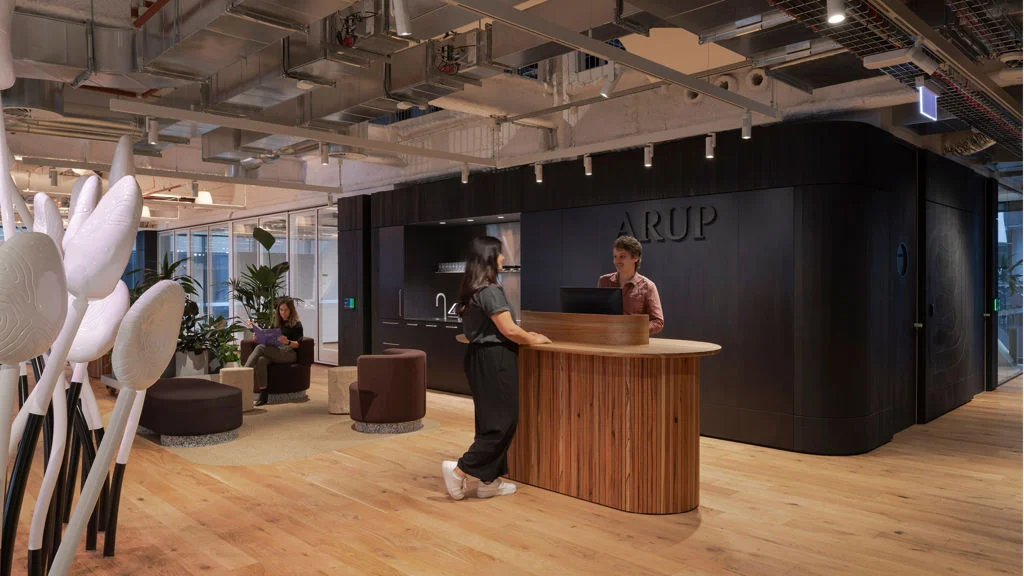
Connecting work, nature and Country
Arup Workplace, WS2, Australia
Get in touch with us
If you'd like to speak to one of our property experts about any of the issues raised on this page or a potential collaboration then please get in touch by completing the form.
