What we delivered
-
Building fire protection into the fabric of the building
-
Developing a safe exit strategy for fire events
-
Optimising the roof structure of Daxing Airport for reduced weight and carbon emissions
Get in touch with our team
The phoenix-shaped Beijing Daxing International Airport has become an iconic building in the Chinese capital.
Designed by Zaha Hadid Architects, ADP Ingénierie and Beijing Institute of Architectural Design (BIAD), the terminal building has a total Gross Floor Area (GFA) of over 700,000m² and can process 100 million passengers every year, relieving pressure on the Beijing Capital International Airport.
Daxing is designed to be a super transportation hub for Beijing. Three underground rail stations with a total area of 200,000 m² are situated below the terminal building, with five railway lines giving passengers transport links for onward travel.
BIAD appointed us as fire engineering consultants for the entire airport, and later asked us to peer review and value engineer the steel roof structure for the Beijing New Airport Construction Headquarters.
The flowing, interconnected form of the terminal is a stunning piece of architecture, but it poses huge design challenges in terms of fire safety. This is complicated by the transportation hub beneath and the interconnecting spaces, which had to be treated as a single massive fire compartment.
Our fire engineers took a performance-based approach to designing the fire control zones for the airport. We incorporated a series of fire protection strategies, including smoke curtains, fire shutters and fire separation bands to prevent the spread of fire and smoke from one zone to another, replacing traditional solid walls that affect passenger circulation.
High risk areas are fully contained with fire resistant construction, and we used the large Central atrium to control smoke by using buoyancy and dilution.


A smart exit strategy
Emergency exits presented a major design challenge. Due to the size and the number of occupants, escape distance to the outside is over 200m for most parts of the Central zone, compared to a standard building where it should be under 75m. To mitigate this, we provided 29 exit stairways in the Central zone, shortening the travel distance for various floors and diverting pedestrian flow to prevent bottlenecks.
The baggage handling areas in arrivals also posed risks for swift evacuation, so we designed a smart exit strategy for public zones using different routes for evacuation depending upon where any fire may be located.

Optimising the roof structure
The roof of the terminal building is a large-span, complex hyperboloid steel grid structure covering over 350,000m². Containing more than 170,000 steel members, it is supported by giant C-shape columns that seamlessly connect with the roof.
Our engineers, using software developed in-house, studied the configuration, loading, vertical support system reactions and the structural deflection and displacement across the roof. 420 load combinations were considered and 38 different cross section sizes were employed in the superstructure, with our analysis showing significant scope for optimisation.
With extensive experience in long span steel structures and structural design, our engineers proposed strategies for the different zones of the terminal, improving roof truss patterns and reducing unnecessary structural depth and member sizing.
Efficiency is the key
Although the design of the steel roof had already been reviewed by several local design institutes prior to our review, Arup’s comprehensive optimisation strategies helped the project achieve a further reduction in steel tonnage, resulting in significant cost savings and reduced carbon emissions.
By integrating the transportation hub and terminal building instead of placing them at separate locations, our solution will help save over 1.6 million hours for nearly 30 million passengers every year.

Did you know?
m2
GFA
m
annual passengers at maximum capacity
steel members for the signature rooftop
ADP Ingeniérie / Zaha Hadid Architects / BIAD / China Airport Construction Co Ltd
Projects
Explore more aviation projects:

Transforming the travel experience at Zayed International Airport
Zayed International Airport Terminal A, United Arab Emirates

Crafting a New York–inspired atmosphere for passengers traveling through JFK’s global gateway to the world
JFK New Terminal One Art, Branding, and Digital Experience Program, United States of America
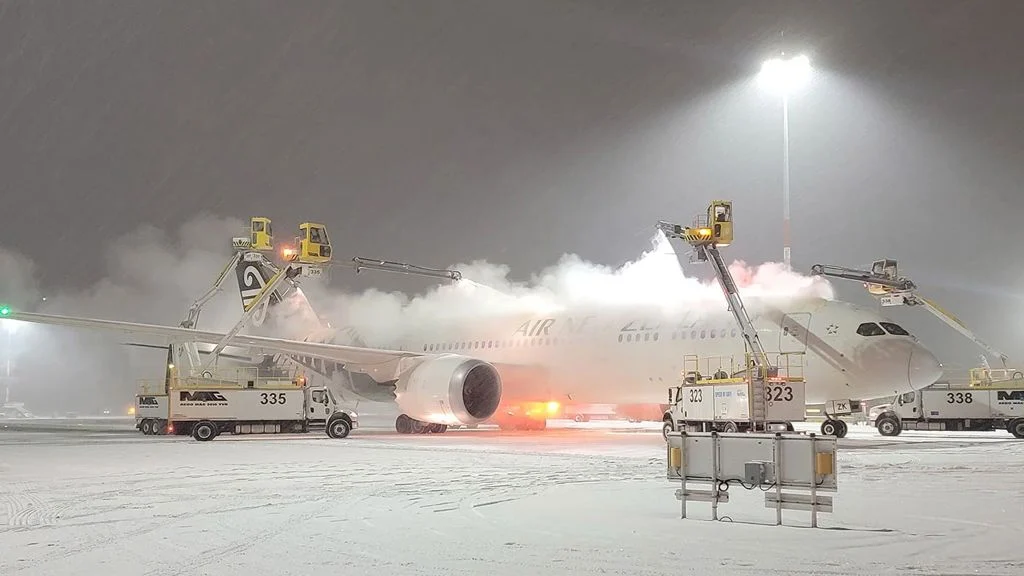
Helping Vancouver International Airport to prepare for unexpected weather
Vancouver International Airport After Action Review, Canada
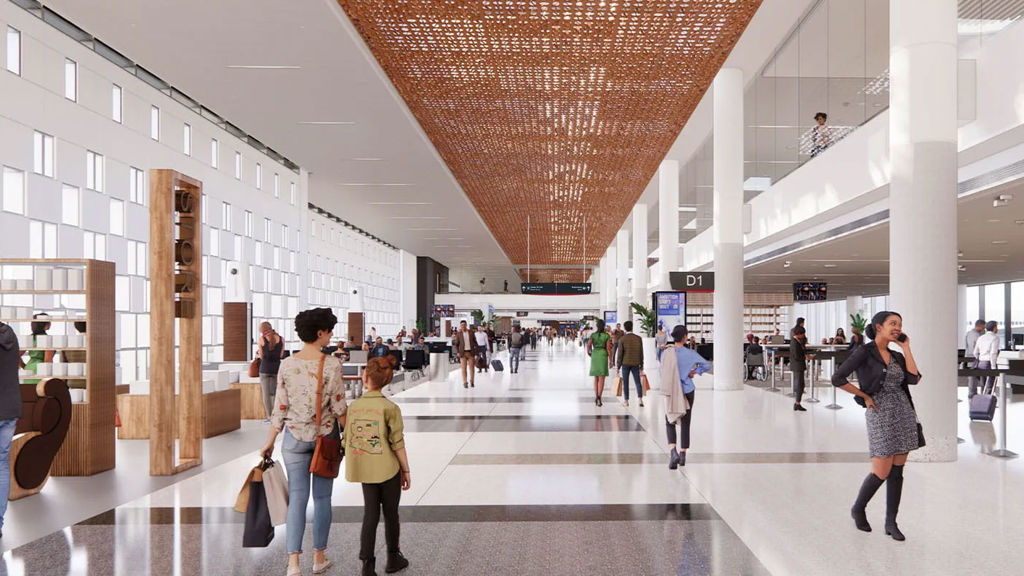
Seamless redevelopment and renovation at George Bush Intercontinental Airport
IAH Terminal Redevelopment Program, United States of America
Get in touch with us
If you'd like to speak to one of our aviation experts about any of the issues raised on this page or a potential collaboration then please get in touch by completing the form.
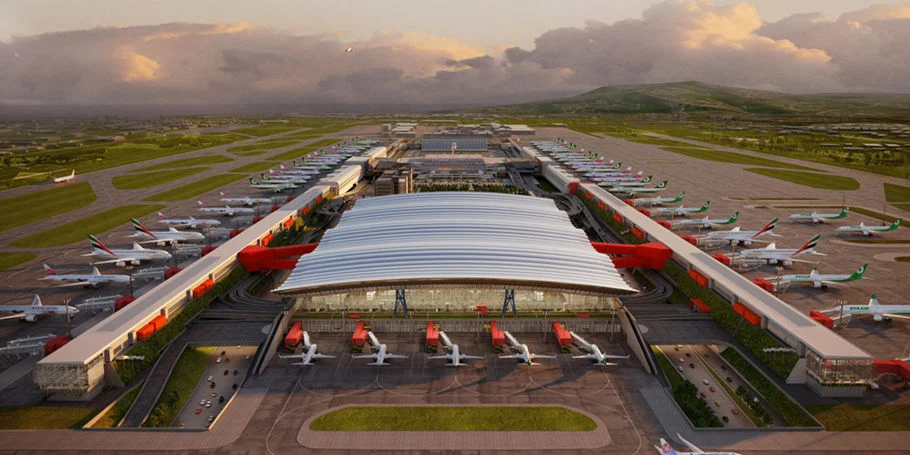