Designing high-performance laboratory infrastructure to foster research collaboration
Pacific Northwest National Laboratory Grid Storage Launchpad (GSL)

As electric grid storage infrastructure becomes increasingly important, Pacific Northwest National Laboratory (PNNL) is evaluating and developing technological solutions to increase resilience and scalability through their Grid Storage Launchpad (GSL). While PNNL explores related chemical processes for electrical storage and material development on its broader campus, the GSL is specifically designed as a testing lab for commercial-scale batteries.
Arup provided mechanical, electrical, and plumbing (MEP) design, as well as fire/chemical process hazard and battery testing consulting services. In these roles, Arup delivered services and control infrastructure to enable safe operations with the testing and validation cells, which are used to evaluate the performance of both commercial and industrial battery technology applied to the electric grid. Arup also developed “template” services infrastructure for the general chemistry labs and connected the GSL to the existing Heat Transfer Building to recapture and reuse waste heat from an adjacent computing facility.
Arup’s work on the project aligns with PNNL’s goals of producing technologies that increase the resilience and capability of the electrical grid in the United States. Additionally, Arup helped ensure that the GSL, especially the battery testing cells, is designed to mitigate a variety of potential risks, and withstand these different scenarios. Overarchingly, the design of the GSL is intended to foster research in a safe, effective manner.
Prioritizing efficiency through a templated approach
A key aspect of the GSL is the recapture and reuse of heat via PNNL’s Heat Transfer Building (HTB). Originally implemented as part of Arup’s work on PNNL’s Energy Sciences Center (ESC), the project team ensured that the GSL was tied into the HTB’s utilities system, which includes a cooling tower and pump house where waste heat is collected from an adjacent data center facility. This heat is then distributed to the GSL, the ESC, and other campus buildings for reuse, resulting in lower heat generation demand in these facilities, as well as enabling a future fully-electrified HVAC system in the GSL.
Additionally, the GSL features an abundance of laboratories, including electron microscopes, nuclear magnetic resonance labs, wet labs, and a low relative humidity lab. The project team developed and implemented a “template” for each of the labs so that the location of all of the equipment could be preorganized, ensuring optimal fabrication and installation, and future proofing later changes to program. The templated approach was coupled with an interstitial utility corridor, which enables safe maintenance access to critical lab utility services without interrupting lab operations.

The GSL operates with a reduced heat generation demand, paving the way for a future fully-electrified HVAC system © Kirksey Architecture

The GSL recaptures and reuses heat via PNNL’s Heat Transfer Building, integrating with a cooling tower and pump house to collect waste heat from a nearby data center © Kirksey Architecture
Enhancing safety through a hybrid approach to battery testing
The GSL facilitates the usage of testing and validation cells, which are bunker-type concrete enclosures where arrays of batteries are tested for performance while connected to the electrical grid. Having these cells separate from the rest of the building works to protect the structure during any potential fire or explosions. Each testing cell contains a test-monitoring area for scientists to observe the performance of a battery remotely, which provides additional safety as the scientists do not have to be in close proximity to the experiment.
In constructing these test cells, it was crucial that they were designed to withstand certain failure scenarios to protect both the PNNL campus and its people. As there is not an existing code framework for the design of battery testing cells, the project team used a basic principles approach to evaluate the explosion risk of various battery types to develop a design basis for the system. The implemented system is intended to prevent a runaway fire scenario and explosion through the use of instrumentation, controls, and ventilation.
Arup also worked alongside the design team to develop a hybrid approach by analyzing the original concept design for the testing cells from an early design phase, in which the methodology to mitigate explosion risk relied on structural hardening and explosion venting. As a team, it was concluded that there was a need for a third layer of mitigation by utilizing an explosion-prevention approach enabled through specialized instrumentation and process exhaust. This approach keeps the gaseous flammable pollutant concentrations in the testing cell below the lower explosive limit. To demonstrate the effectiveness of this approach, Arup performed Computational Fluid Dynamics (CFD) modeling of the testing cells and provided the client with the CFD models so that they could be adjusted in the future as battery technologies change. These analyses can also be used as a safety modeling tool for PNNL’s future experiment setups. The project team also leveraged the expertise of global colleagues on Arup’s Functional Safety team to help certify the safety instrument system (SIS), which was a key component of the explosion prevention system design.

The GSL features an abundance of laboratories, including electron microscopes, nuclear magnetic resonance labs, wet labs, and a low relative humidity lab © Kirksey Architecture
What we delivered
-
Established a design basis for battery testing cells that prevents potential runaway fire scenarios
-
Implemented a recapture and reuse heat transfer system to lower heat waste and ensure minimized heat generation demand
-
Developed a template lab services configuration to ensure that each lab space is preorganized to accommodate future equipment
Get in touch with our team
Projects
Explore more science projects
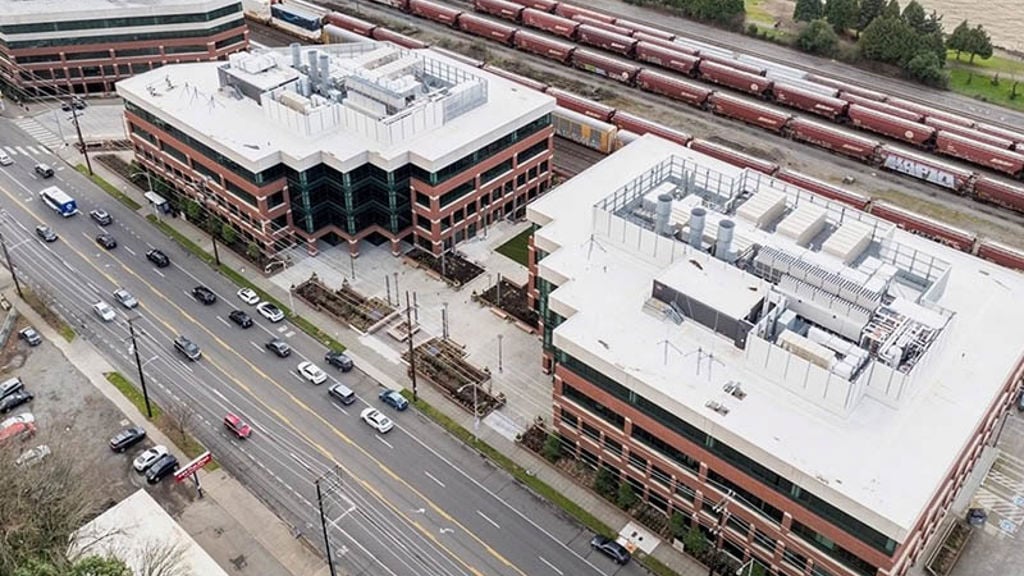
Employing adaptive reuse to support Seattle’s growing life sciences industry
Unison Elliott Bay, USA
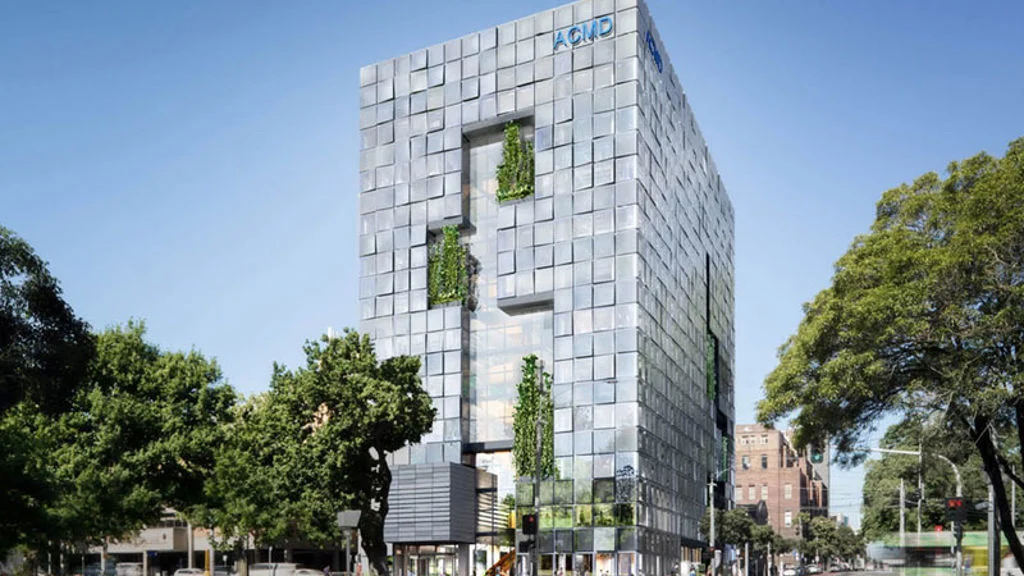
A new hospital-based research centre for greater collaboration
Aikenhead Centre for Medical Discovery, Australia

State of the art gene bank embodies flexibility and sustainability
International Center for Tropical Agriculture – Future Seeds, Colombia

Advising Max Planck Society on the development of a new research campus in Munich
Max Planck’s Martinsried campus development, Germany