Engineering business resilience: pharmaceutical production upgrade programme for life sciences leader
Pharmaceutical Production Upgrade

What we delivered
-
Leveraging global expertise to assess and deliver a worldwide production upgrade for a leading pharmaceutical company
-
Collaborating at every level to create a system of excellence in the design and build of advanced scientific facilities in multiple locations
-
Modelling data for optimal performance and assessment of asset functionality that can be shared across a global production portfolio
Get in touch with our team
At Arup, every project we work on is driven by consistent collaboration and engineering excellence to achieve the goals of our clients. This project, working with a leading international pharmaceutical company, demanded an extremely high level of both in order to deliver a world class solution for their global business, without interrupting vital production.
As one of the most regulated industries in the world, pharma and life sciences companies require a reliable, consistent approach to manufacturing across all their production facilities. But how do you design and roll out a global programme to upgrade pharmaceutical production facilities for one of the world’s top life science groups whilst minimising production disruptions?
To future-proof its business, our client wanted a global partner to design and implement a production facilities upgrade programme to deliver technical standardisation and improved production resilience worldwide. Arup was initially appointed to carry out a gap analysis and engineer design solutions for seven sites across Europe, Asia and the Americas in 2016, providing global programme management as well as cleanroom and life sciences expertise.
Building on this initial collaboration, the programme was extended to cover 33 of the firm’s production facilities. Our scope expanded to include the creation and roll-out of a global BIM strategy, and support with technical standardisation and knowledge management. During the course of the programme, our specialists developed design concepts for about 270,000m² of clean room area – equivalent to around 38 football pitches.
Collaboration is the key to unlocking long term value
Focused on quality, consistency and standardisation, our collaborative relationship with the client has enabled us to respond to a fast-moving corporate landscape, quickly adapting and responding to the client’s evolving strategy.
Building a truly integrated relationship from the outset was key for the success of the global programme. Our approach included the creation of a multi-disciplinary working team to bring together the client’s commercial, engineering, quality and production specialists with our own experts. This collaborative approach helped the whole working team gain a better understanding of each facility’s specific requirements. This in turn has minimised production shutdowns during implementation and helped secure alignment for mitigating measures.
Knowledge management – a global view
Data and knowledge management was essential to the success of the programme, with our specialists working together to develop concepts, share information and standardise methodologies across 33 different sites.
To coordinate the many Arup offices and specialists working on the programme, including project managers, multi-disciplinary engineers, and specialists consultants across Germany, Ireland and the United States, we developed a series of tools and methodologies to ensure alignment, helping us quickly incorporate the lessons learnt to deliver continuous improvement for the client.
After review with the multi-disciplinary working team along with feedback from a range of client stakeholders, some of the standardised deliverables, workflows and methodologies developed for this programme have been adopted by the client.
Inspecting 33 sites worldwide
Working with the client, we inspected 33 production facilities worldwide using our proprietary site inspections tablet app. As all the sites were fully operational, collaboration with the local engineering and production team was essential to develop the design and ensure that constructability and phasing minimised impact on production.

Developing designs with BIM at the forefront
The design concepts mainly focused on cleanrooms and mission-critical systems like the Heating, Ventilation and Air Conditioning (HVAC), EMS (Environmental Monitoring Systems), BAS (Building Automation Systems), Pressure Cascades and Airlocks for both staff and materials.
Driven by the priorities at each site, the scope of the programme often evolved to include further critical topics, for example building envelope analysis, fire protection, seismic studies, utilities and process flow improvements as well as CFD simulations – all of which was delivered in BIM.
Meeting global technical standards
To simplify approvals and provide better insight for quality assurance teams, the multi-disciplinary working team developed a framework of standardised deliverables usable across the client’s global portfolio. The team developed a total of 17 Technical Standard documents, which have now become mandatory for all the client’s engineering projects. Detailing best practice for the fit-out of cleanrooms and air locks, layouts for several specific room types, as well as HVAC systems and pressurisation concepts, the documents offer examples of how GMP requirements can be planned and implemented in practice.
Global BIM consultant
As global BIM consultant, we continue to work with the client to implement standardised BIM methodology, including the creation of BIM guidelines and Revit Start Configuration files.
We are also helping with the implementation of BIM standards, processes and templates in projects and across sites, as well as supporting with the planning, procurement and roll-out of an Engineering Document Management System (EDMS) to help with global standardisation, archiving, maintenance and processing of all project data.
Leveraging data and digital tools for the long term
The huge amount of site data and information gathered and generated during the programme has been consolidated into a series of central databases, benchmarks and BIM models to ensure the client can continue to derive value from the efficiencies achieved - even after the programme is complete.
Our contribution to the success of this project has also included developing a range of intuitive online engineering tools based on this data, including a digital Global Manufacturing Practice compliance checker currently in pilot phase, as well as design and cost estimation tools for Personnel Air Locks (PALs) and Environmental Monitoring Systems (EMS).
Sustainability: Developing an energy management dashboard
By leveraging data generated during the programme, our consultants are also helping the client with Energy Management. Started in spring 2020, the cleanroom energy usage of the sites is captured in data models that take into account the local climate, GMP specifications and Air Handling Units (AHU) component configurations.
As the number of data models grows, our client will have a powerful tool showing an interactive comparison of energy performance across its global portfolio. The insights provided by these data models will support the life sciences leader in its ambition to become carbon neutral by 2030, enabling the company to make informed strategic decisions on its sustainability journey.
Carpus + Partner AG / Wilson Architecture in Cork / Wilson HGA in Boston
Projects
Explore more science projects

Shaping the future of research environment
Innovent Biologics Global R&D Center, Mainland China
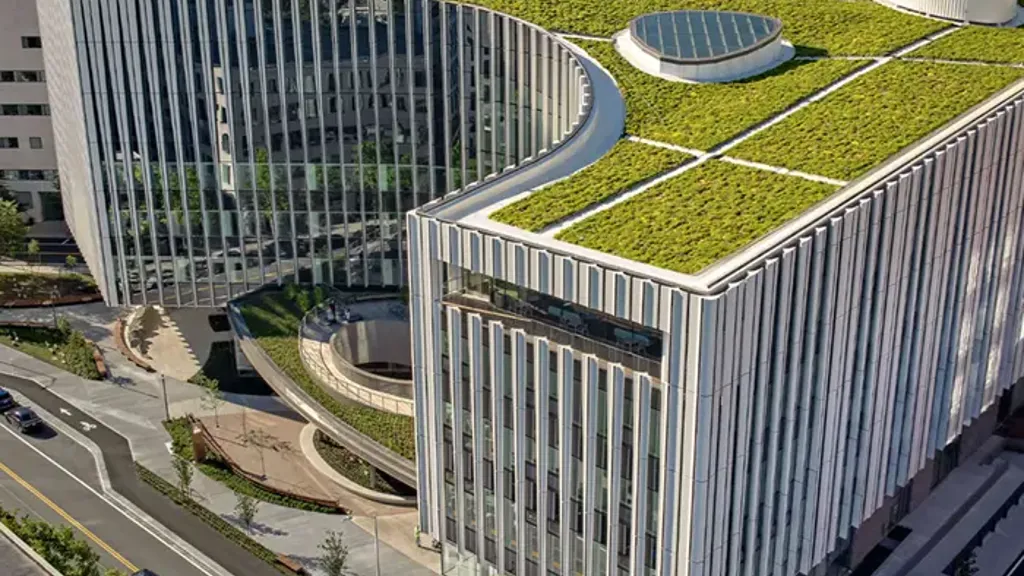
A space for life-saving research
Ragon Institute, United States of America

Designing high-performance laboratory infrastructure to foster research collaboration
Pacific Northwest National Laboratory Grid Storage Launchpad (GSL), United States of America
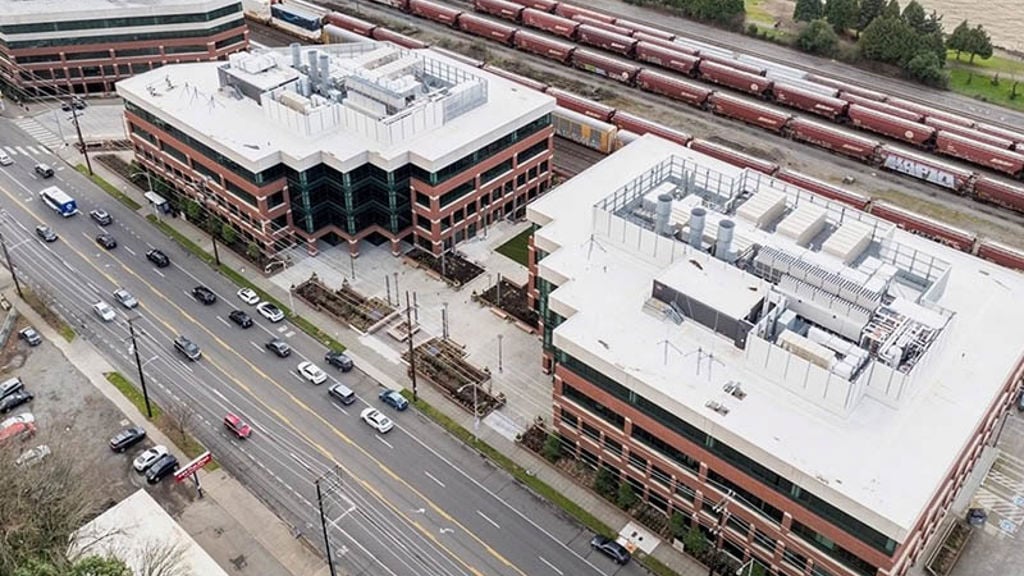
Employing adaptive reuse to support Seattle’s growing life sciences industry
Unison Elliott Bay, United States of America
Get in touch with us
If you'd like to speak to one of our science experts about any of the issues raised on this page or a potential collaboration then please get in touch by completing the form.
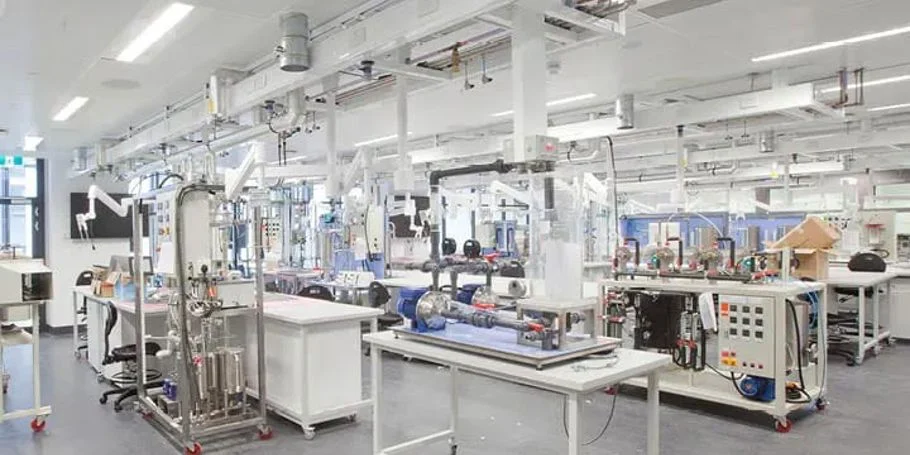